CNC precision machining is the process by which raw material is shaped into a finished product by cutting out excesses designated by a Computer-Aided Design (CAD) or Computer-Aided Manufacturing (CAM) blueprint. The process is broken up into two types: subtractive and additive manufacturing. These processes are used in different manufacturing processes and on different materials.
Precision machining is used for many parts, including metal components for automobiles, aircraft, and other vehicles and components for electronics, medical devices, and other products. The process may be used to create simple parts or complex assemblies made up of multiple components.
CNC precision machining involves using computer-controlled tools to cut away material from a workpiece to create the desired shape. In this process, the CNC machine operator can control only two variables — time and feed rate —. Other variables like depth of cut and tool engagement aren’t as easy to control on manual machines because they require more skill than required when using a CNC system.
The tools used in this process typically include drills, milling cutters, and grinding wheels; however, these tools can also be replaced with lasers or water jets, depending on what type of material you’re working with.
Tolerance of Precision Machining
The tolerance of precision machining can be defined as the difference between the maximum and minimum dimensions permitted in a given set of drawings. Tolerances are specified by the designer or engineer who creates the drawing.
Tolerance is expressed as a percentage of the basic dimension, usually the nominal size (the size stated on the drawing). The tolerance can also be expressed in terms of a fractional amount, such as 0.125, meaning 1/8″ or 0.125″ (1/8″). This fractional amount must be multiplied by two to get the actual amount of tolerance. For example, if you have a part with a nominal size of 5 inches and want your tolerance to being plus or minus 0.025 inches. You will have to allow for a plus or minus 0.05-inch variation in size (5 x 0.025 = 1/2″). The actual allowable variation would then be plus or minus 0.05 x 2 = 1/4″.
The total allowable variation is called the “total allowable error” (TAE), and it consists of two parts: one part due to manufacturing tolerances and one part due to geometric tolerances (or geometric form). The first part is related to machining methods and tools used in manufacturing, and the second is related to the shape of the manufactured part.
The total allowable error may be specified as a decimal value, such as 0.05. This means a maximum allowed deviation of 0.05 inches for every inch length (or diameter) of the part being manufactured.
There are different types of tolerance measurement systems. For example:
Standard Tolerance Measurements – These are the most common CNC tolerance measurement systems. They use fixed-position sensors to measure the part. The part is placed in a fixed position and requires no special setup or preparation before measurement. However, these systems do not allow for any part orientation or size variation.
Variable Offset Tolerance Measurements – These types of CNC tolerance measuring systems use an offset measurement system, meaning they do not require the part to be placed in a specific location. They use a single sensor to measure multiple locations on the part at once, meaning there is no need to move parts around when performing measurements. This makes them valuable for production environments where parts may need to be measured quickly and efficiently without requiring multiple setups or toolsets.
Dynamic Tolerance Measurements – CNC tolerance measuring systems use dynamic motion rather than static positioning to make measurements. This allows them to make measurements without requiring preparation from the machine or operator before making measurements (such as moving things into place). However, this also means that it must be properly calibrated before being used to measure parts properly. This makes them more accurate than static systems, but they are also more expensive and require more time to set up.
Types of Precision CNC Machining Equipment
Precision CNC machining is quickly becoming a means to create high-quality precision parts. With this in mind, it makes sense that many companies want to know what types of machines they can utilize within their facilities to get the job done. There is a larger variety than you might think.
Lathes
Lathes turn metal into cylindrical shapes or perform other operations like threading and drilling holes. Lathes have been around for thousands of years and have changed little over time. They’re still widely used in industry today because they produce high-quality results while providing great control over the finished product. Lathes come in both manual and automated forms, but all lathes follow the same basic design principles no matter what type they are.
Milling Machines
Milling machines can perform many different functions depending on the tools attached to them (tool holders). They can be used for milling, drilling, reaming, threading, tapping, and much more. Milling machines often create complex parts requiring multiple actions during production, such as threading and drilling holes at different depths into a single piece of metal. They commonly manufacture gears and small parts requiring precise measurements and angles.
Grinders
Grinders are machines that use abrasive wheels to grind metal. They can be used to shape, remove material and deburr parts. Grinders are primarily used in the automotive industry and often remove excess material from a part after it has been cut with other machines. The most common type of grinder is a surface grinder with four basic components; the spindle, table, headstock, and. tailstock.
Drill Press
A drill press is used to drill holes into metal or other materials. Drill presses come in various sizes, ranging from small bench-top models to large floor-standing machines. A drill press can be used with various cutting tools such as drills, reamers, and milling cutters. The drill press uses an indexing table to move the workpiece into position so that each hole can be drilled at the correct angle and depth. Some models also have adjustable depth stops that allow users to set precise hole depths for precise alignment of parts during assembly.
CNC Laser Cutting Equipment
CNC laser cutting machine is a device that can automatically cut various materials, such as metal, plastic, and non-metallic materials. It is widely used in electrical appliances, automobiles, shipbuilding, and other industries.
CNC laser cutting equipment mainly consists of a computer control system, a laser source, and a cutting head. The computer control system includes an operating system and various software modules. The operating system is responsible for controlling the entire process of cutting. The software modules help to realize the functions such as loading files into memory, executing cutting programs, and monitoring the status of the CNC laser cutter machine.
To improve their cutting accuracy and productivity, CNC laser machine adopts high-speed digital processing technology and intelligent control technology (such as PLC). The structure of the main components is rationalized using a modular design concept so that they are easy to install and maintain.
CNC Electric Discharge Mining Equipment
Electric discharge machining (EDM) is a subtractive process that uses electrical discharges to cut, shape, and etch materials. A direct current (DC) electrical discharge machining process is used to cut soft materials such as copper and aluminum. An alternating current (AC) electrical discharge machining process is used to cut harder steels, stainless steels, and other similar alloyed metals.
In EDM, a high-voltage spark is generated between two electrodes in the material being machined. The amount of spark energy determines the depth of penetration into the material. The electrode with the highest voltage is called the hot wire, while the lower voltage electrode is called the tool or probe.
CNC Precision Machining Applications
Precision Machining is gradually gaining more ground in the manufacturing world due to its multiple uses and time-effective processes. The precise machining process is used in the aerospace, automotive, marine, and transport industries.
Medical Industry
CNC precision machining is used extensively in the medical device manufacturing process. Medical devices come in all shapes and sizes, from simple bandages to complex surgical instruments. All these devices must be carefully designed and manufactured to meet specific requirements. CNC precision machining plays an important role in this process because it allows manufacturers to produce high-quality products on time, which could not be done without this technology.
Automotive Industry
The automotive industry is one of the most important industries in the world. It is a very competitive business, and every company wants to have a unique product that stands out from others. The industry uses CNC precision machining applications to manufacture parts with high accuracy, efficiency, and quality to achieve this goal.
The automotive industry uses CNC precision machining applications for many purposes, such as manufacturing parts for different vehicles (cars, trucks, buses, etc.), making engines and other engine parts, producing navigation devices, and many more.
Aerospace Industry
The aerospace industry is another sector where CNC precision machining applications are widely used. This industry uses CNC machines to manufacture aircraft parts by cutting metal plates or sheets into desired shapes using computerized control systems, which makes them highly accurate and efficient. The aerospace industry mainly produces aircraft components such as wings, fuselage sections, etc., made from aluminum and titanium alloys. These components are then assembled to form airplanes or helicopters etc.
Military and Defense Industry
Military and defense companies have been using CNC precision machining applications to produce parts used on aircraft, missiles, ships, and submarines. These parts are made of different alloys that must be machined precisely, like titanium or aluminum alloys. The tolerances range from ±0.001″ up to ±0.0001″ depending on what type of part needs to be produced by these companies.
Advantages Of High Precision CNC Machining
CNC machining is a process that uses computer-controlled machines to cut and shape the material. CNC machining is used in manufacturing industries to create parts that are too complex to be produced using traditional methods. The use of CNC machines has many advantages over the manual process, such as:
Reduced cost of production
CNC machining requires less time than manual machining, which reduces the overall cost of production. This is because fewer workers and less time are required for setup and changing tools. In addition, there are fewer errors and reduced material waste during the process.
Improved accuracy
CNC machines provide better accuracy due to their high-precision capabilities and accuracy levels that can be easily programmed into computer software. The accuracy level depends on the machine used, with milling machines offering higher precision levels than turning or grinding machines. The CNC machines also allow you to program multiple operations into one file using different tools and speeds, which allows you to achieve better results in less time.
Increased speed
CNC machining can produce many parts faster than any other method. It’s one of the fastest ways to manufacture metal parts. The high speeds allow you to produce more parts in less time, which translates into higher productivity for your business.
Precision
High precision is one of the main benefits of using CNC machines over other methods like manual assembly or stamping operations because they offer more control over how much material is removed from each part. This ensures that every unit meets quality standards and is identical to all others made on the same machine, making it easy for people to find replacement parts if necessary.
Cost
The cost of using CNC machines is much lower than other methods like manual assembly or stamping operations since they require less labor. This is especially beneficial for businesses that manufacture large parts because it allows them to make more profit with each sale.
How to Carry Out Precision Machining
Materials
CNC precision machining is a process that uses computer numerical control to cut materials with high precision. The most common materials for CNC precision machining are metal, plastic, and wood.
Metals
Metals are the most common materials for precision machining. Metals are strong and durable and can be machined with high accuracy.
Aluminum is one of the most common metals used in precision machining. It’s relatively light, easy to machine, and inexpensive compared to other metals. Aluminum is also resistant to corrosion and oxidation, so that it can be used in harsh environments like marine and aerospace applications.
Stainless steel is another common material for precision machining because it’s strong and resistant to wear and tear. However, stainless steel can be difficult to machine because its hardness makes it brittle and prone to cracking or chipping during machining operations.
Titanium is a strong metal with good tensile strength and high melting point; however, it’s so expensive that it’s rarely used for precision machining purposes except by aerospace manufacturers with very deep pockets!
Magnesium is another lightweight metal with many applications in the aerospace, automotive, and marine industries. Its lightweight and high-strength properties make it ideal for use in these applications. Regarding parts or structures, weight reduction is an important factor.
Plastics
Plastics are the most common material used in CNC precision machining. Many plastics are compatible with CNC machining, including:
ABS is a popular choice because of its high impact resistance and strength, but it has a poor heat resistance and dimensional stability. It can be molded into parts with high precision tolerances and has a good surface finish, making it ideal for parts that must fit together tightly.
PC is almost identical to ABS in terms of mechanical properties but has better thermal stability. This makes it a good choice for applications where temperatures vary widely between suppliers or environments, such as automotive parts that need to withstand extreme temperature changes over their life cycles.
PMMA (also known as acrylic) is used in many consumer products due to its transparency and scratch resistance. Still, it’s not usually used in injection molding because it’s hard to get consistent quality results when producing large volumes.
POM (polyoxymethylene) is commonly used for gears due to its high strength-to-weight ratio, low coefficient of friction, and excellent wear resistance. Its main drawback is that it tends to warp during cooling from elevated temperatures, which requires special tooling design considerations.
Programming
A CNC programmer is a person who writes the program code to control a computer-controlled machine tool. The programming process typically occurs on a CAD/CAM system linked to the machine tool.
Programming requires knowledge of machining processes and how to write software in one or more programming languages.
Programming CNC machines requires knowledge of how to program in G-Code and code for specific types of machines.
Programming with G-Code is similar to writing human-readable programming code like BASIC, Pascal, or C++. However, there are some important differences between the two types of code. For example, G-Code uses special “commands” that tell the machine what operation needs to be done (such as cutting an outline into metal). These commands are usually placed inside curly brackets ({ }).
Some CNC machines have graphical interfaces that allow them to be programmed without G-Code!
Processing
We provide precision machining services in our state-of-the-art facility. Our precision machining capabilities include the following:
• Precision CNC milling
•Precision CNC turning
• Precision CNC drilling and boring
• Precision EDM (electrical discharge machining)
Our precision machining capabilities are used to create the following products:
• Custom injection molded parts, including 2D and 3D features and colors
• Custom castings with select materials, including aluminum and magnesium alloys, as well as other metals such as steel, brass, and bronze
• Metal stampings for hardware applications
Surface Finishing
The surface finishing of a product is the last step in its production process. This process involves polishing, buffing, and applying protective coatings to the final product. This process aims to enhance the product’s aesthetic appeal while protecting it from wear and tear.
Surface finishing is used in several industries, including automotive, medical equipment, jewelry, and space exploration. It’s an important part of making any product look good and last longer.
CNC Precision Machining is the best way to ensure that your machined parts are as accurate and precise as possible. For more information on this process, contact us today!
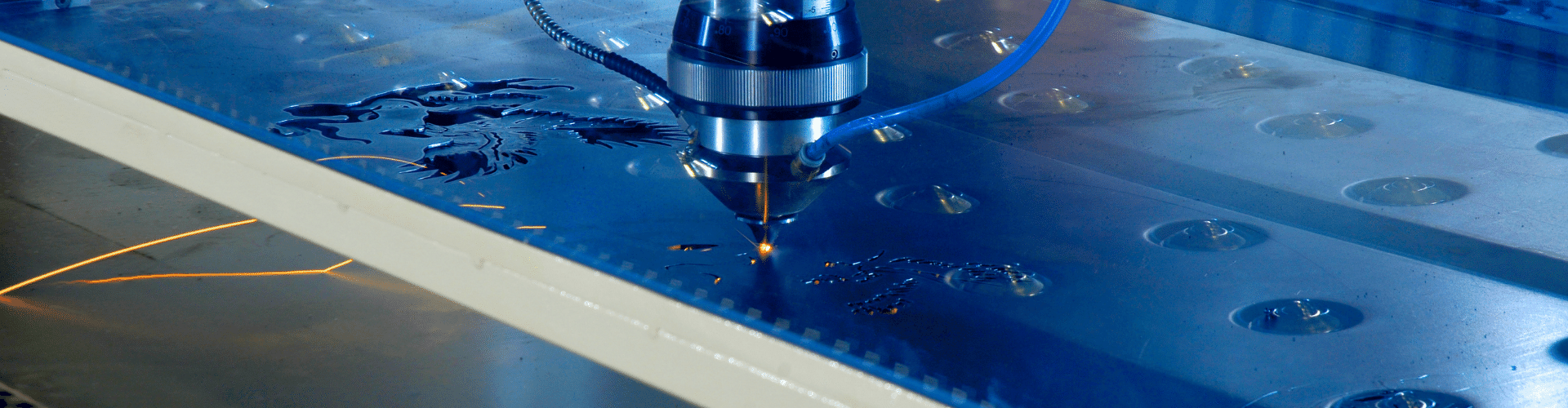
Need quality cnc machining service in China
As a full-service precision machining house, ETCN has been offering CNC machining to customers with precision machining and high quality service.